Latest Industry News Briefs Courtesy of PMTA
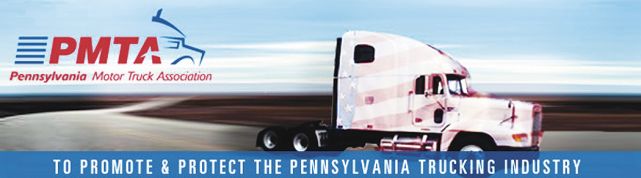
ATA Truck Tonnage Index Rose 0.5% in August
Arlington, VA… American Trucking Associations’ advanced seasonally adjusted (SA) For-Hire Truck Tonnage Index increased 0.5% in August after falling 1.1% in July. In August, the index equaled 110.3 (2015=100) compared with 109.8 in July.
“August’s monthly gain, while small, was the first since March,” said ATA Chief Economist Bob Costello. “It is important to remember that ATA’s tonnage data is dominated by for-hire contract freight, with a very limited amount of spot market freight. I continue to believe that tonnage has not recovered to pre-pandemic levels for two main reasons - broader supply chain issues, like semiconductor shortages, as well as industry specific difficulties, including the driver shortage and lack of equipment.
“Despite some supply chain issues, demand remains strong for trucking services generally. Truckload carriers are operating fewer trucks than a year earlier, which makes it difficult to increase freight volumes significantly,” he said.
July’s reading was revised up slightly to -1.1% from our August 24 press release.
Compared with August 2020, the SA index fell 0.5%, which was the second straight year-over-year drop. In July, the index was down 2.9% from a year earlier. Year-to-date, compared with the same eight months in 2020, tonnage is down 0.2%.
The not seasonally adjusted index, which represents the change in tonnage actually hauled by the fleets before any seasonal adjustment, equaled 114.5 in August, 2.2% above the July level (112). In calculating the index, 100 represents 2015. ATA’s For-Hire Truck Tonnage Index is dominated by contract freight as opposed to spot market freight.
Trucking serves as a barometer of the U.S. economy, representing 72.5% of tonnage carried by all modes of domestic freight transportation, including manufactured and retail goods. Trucks hauled 11.84 billion tons of freight in 2019. Motor carriers collected $791.7 billion, or 80.4% of total revenue earned by all transport modes.
Bendix Tech Tips: Troubleshooting And Diagnosing Advanced Safety Systems
ELYRIA, OH… A dashboard warning light can send a simple and clear message: Something on your truck needs to be checked. But on today’s complex vehicles – and particularly when it comes to their increasingly interconnected safety systems – knowing exactly how and what to check can mean the difference between hours and days of costly downtime.
This installment of the Bendix Tech Tips series provides guidance on troubleshooting and diagnosing advanced safety technologies, from the foundational elements of antilock braking to the components that enable collision mitigation and more.
Start Simple
“Sometimes the first response to an indicated electronics problem within collision mitigation systems may be to start removing and replacing components,” said TJ Thomas, Bendix director of marketing and customer solutions – Controls. “But there are plenty of times when a component isn’t the issue, so we recommend starting by running a diagnostic software tool that shows a system view of what’s on the vehicle that includes key vehicle components as well.” This assessment can give the technician a quick overview of what’s going on, especially when more than one component shows similar active DTCs, such as J1939 communication errors.
The technician can also look for frayed wires, corroded connectors, or blown fuses. Additionally, equipment like cameras and radars should be checked to make sure they’re unobstructed by things like road debris, snow, and ice.
In addition, some DTCs are “self-clearing,” Thomas said. “This means that simply by fixing the situation – removing the obstructing debris, for instance – the indicator lights and associated fault codes will be deactivated.” Service data sheets should call out these types of DTCs so the technician can be aware of what kinds of conditions generate them.
If this initial approach comes up empty and it looks like the problem is something a bit deeper, then having the right tools and the know-how to use them is the key to getting trucks back on the road and in good working order as quickly as possible.
It’s All Connected
More than ever, the various systems across a commercial vehicle are intertwined, with multiple electronic control units (ECUs) sharing necessary information over the J1939 network. For example, automated transmissions depend upon information from the engine to operate properly and at their highest efficiency.
“Seemingly everything on these trucks is talking to everything else,” said Brian Screeton, Bendix supervisor – Technical Service Training. “So, the best tip we can give for diagnosing faults in higher-level safety systems like adaptive cruise control is to make sure you’re looking at the entire truck first.”
“If a driver reports an adaptive cruise fault, then a technician might connect their diagnosing tool just to the radar, and there may not be an active fault there, but they wind up going down a rabbit hole and spending time trying to troubleshoot inactive faults, when really it turns out there’s an engine problem driving the whole thing. Faults in one system can be driven by a completely separate system component.”
A J1939 fault, for example, will impact several systems, so a technician should investigate that fault first, then re-run the diagnostic tool to see if the individual system faults are cleared up. Because of that possibility, Screeton emphasized that before making any changes to a vehicle, technicians should run a comprehensive Diagnostic Trouble Code (DTC) report as a benchmark, to know the vehicle’s full status before beginning work.
The Right Tools
Before assuming that an advanced safety system active DTC means something is wrong with that system, technicians should make sure they’re using a tool that gives them visibility to any active DTCs being broadcast on the vehicle’s J1939 network. Bendix® ACom® PRO™ is one such tool, but the important thing is having a diagnostic tool that shows DTCs of the full vehicle.
“A tool that shows you an active DTC on the engine retarder, for instance, tells you that you need to troubleshoot that issue first, because it may be the cause of your adaptive cruise control DTC,” Screeton said. “In fact, we recommend technicians always troubleshoot any active engine faults first because of the way they impact other system faults.”
When connected to a vehicle, the ACom PRO software automatically detects and gathers active and inactive DTCs from all Bendix electronic control units on the vehicle, as well as key vehicle ECUs, like the engine and transmission. This roll call shows what’s on the vehicle, eliminating the need for a technician to guess from a prepopulated list of components.
Addressing ADAS
Advanced driver assistance systems (ADAS) that offer capabilities like adaptive cruise control and automatic emergency braking are deeply integrated through their communications with systems like the brakes, engine, and transmission. They also include their own ECUs and sensors like camera and radar units – components that require an extra degree of caution.
“Physical components of stability and collision mitigation systems generally require maintenance only if changes have been made to certain parts of a vehicle. If you do a front-end alignment or work on the steering linkage, for example, then you’ll need to recalibrate the steering angle sensor according to the manufacturer’s guidelines,” Thomas said. “Before a technician adjusts a camera or radar, we stress that they address any J1939 faults or engine faults first. You don’t want to have to take time replacing or realigning a sensor if it’s not necessary.”
Additionally, modern diagnostic tools increasingly have the ability to make changes to systems, from calibration to reconfiguration. Bendix strongly recommends that any individual technician should confirm with maintenance or fleet management before making any performance changes to ensure the result will be consistent with what the fleet wants.
Staying Up to Date
“One other thing that we get feedback on from fleets is the value of ongoing training,” Screeton said. “We have our Brake School sessions where we talk about how these systems work and how our diagnostic tools work, and in addition, providing know-how. It really showcases the importance of regular check-ins with manufacturers and suppliers about the latest information on products and maintenance methods.”
CVSA Transitions to New Leadership for 2021-2022
The Commercial Vehicle Safety Alliance (CVSA) transitioned to new leadership for 2021-2022 today. This effective date reflects the membership’s April 2021 vote to align the transition to new leadership with the fiscal year, which starts on Oct. 1 every year.
Capt. John Broers, with the South Dakota Highway Patrol, is the new president of the Alliance. Maj. Chris Nordloh, with the Texas Department of Public Safety, is CVSA’s vice president. And Sgt. John Samis, with the Delaware State Police, moves into his three-year commitment as past president.
This year’s transition was unique. In June 2020, due to the COVID-19 pandemic, the CVSA Board of Directors voted to cancel the 2020 CVSA Annual Conference and Exhibition. According to the Alliance’s bylaws, if the annual conference is canceled, leadership officers and committee and program members continue in their respective positions until the next annual conference, which was in August-September 2021; therefore, members of leadership with expiring terms served an additional year.
Since the 2020 annual conference was canceled and term expirations were extended by a year, there was no secretary vote in 2020. Instead, the secretary vote took place at the 2021 CVSA Annual Conference and Exhibition. Col. Russ Christoferson, with the Montana Department of Transportation, was elected by the membership on Sept. 1 to the position of secretary, effective immediately.
Col. Russ Christoferson will serve one year as secretary of the Alliance, while concurrently serving as chair of the CVSA Election Committee. Then, he’ll concurrently serve a year as vice president and chair of the CVSA Finance Committee. The year after that, he will become CVSA’s president. After one year as president, he will then serve three years as past president – making the entire obligation a six-year commitment.
In addition to the executive leadership transition:
* The new president of Region I is Tpr. William Alarcon, with New Jersey State Police. The new vice president is Tpr. James Thomas, with Rhode Island State Police.
* Bart Teeter, from the Texas Department of Public Safety, is Region II president and Lt. Ron Jenkins, of the Oklahoma Highway Patrol, is the vice president.
* Maj. Jon Smithers, with the Indiana State Police, takes over as Region III president. Nebraska State Patrol’s Lt. Mike Maytum is the new vice president.
* Brad Marten, with the Montana Department of Transportation, is the new Region IV president, and the new vice president is Tpr. Jeremy Disbrow from the Arizona Department of Public Safety.
* Newfoundland and Labrador’s Krista Cull will serve as vice president for Region V.
* Ofc. Lincoln Sweeney, with the Cedar Hill Police Department in Texas, is the new vice president for Class II Local Members.
* Andrea Sequin, with Schnieder, is the new president of Class III Associate Members and Derek Barrs, from HNTB, is vice president.
* Capt. Jonathan Olsen, with Minnesota State Patrol, will chair the Operation Safe Driver program, and Lt. Col. Michael Krumm, of Michigan State Police, will chair the Human Trafficking Prevention program.
CTA Spells Out How Supply Chain Can Limit Disruptions
TORONTO, CANADA… Canadians are wondering if recent disruptions in the European supply chain can also occur here.
More than any other time in recent memory, Canadians have come to appreciate and understand that our nation’s economy moves by truck and truck drivers are critical to keeping our factories open and stores shelves full.
The Canadian Trucking Alliance, which represents over 5,000 Canadian motor fleets, wants to assure the Canadian public that our industry and professional workforce are cooperating with customers and all levels of government through the pandemic to ensure all Canadians continue to have access to all the products and essential goods our economy depends on.
This is not to dismiss the challenges the Canadian supply chain faces – because they are indeed very real. The Canadian supply chain has been fragile throughout the COVID-19 crisis and some uncertainty persists, but with businesses and governments working together we can overcome many of these challenges to safeguard against widespread disruptions while emerging from these extraordinary times with a stronger and safer truck transportation sector.
There is no escaping the fact the trucking industry is facing a significant labour shortage of commercial drivers. According to Trucking HR Canada, there were nearly 20,000 vacant truck driver positions this year. Even before COVID-19 emerged, the trucking industry already faced a sharp labour crunch. A pre-COVID report published by the Conference Board of Canada found that there could be 30,000 to 40,000 jobs vacancies for Canadian truck drivers by 2023.
The pandemic has only made this capacity crunch worse as more drivers – already one of the oldest workforces in Canada – increasingly choose to retire.
The labour shortage has also extended to other critical industry positions, like heavy truck mechanics, which is causing longer periods of downtime for equipment in need of repair. Additionally, the industry is currently facing a shortage of pre-owned equipment and significant delays in new equipment deliveries for trucks and trailers. Wait times for new equipment – currently between eight months and over a year – is more than three times longer than normal. Furthermore, the lack of equipment is creating issues for shippers in the supply chain who rely on trailers as mobile warehouses to store preloaded goods for pickup.
There are several actions the industry is taking to mitigate the combined disruptions and economic impact caused by labour shortages, including a national recruitment campaign to attract a new generation of workers; ongoing training; competitive compensation packages and flexible work schedules and giving drivers power over deselecting customers who treat drivers poorly and unnecessarily detain drivers and waste their limited time at loading docks.
Companies purchasing trucking services who do not want drivers to deselect them can be ‘shippers of choice’ and limit potential service disruptions by eliminating as much detention time as possible, loading unloading in a timely manner and treating drivers with respect.
Meanwhile, the government can act in several ways:
* Trucking receives a much smaller share of training funding than other related sectors. CTA is calling on the federal and provincial governments to provide known, trusted trucking companies greater access to training dollars to assist a new generation of Canadians in becoming safe and compliant commercial vehicle operators;
* Trucking also has very limited access to foreign labour. With declining birth rates in Canada, trucking, like all sectors of the economy, will rely on new entrants for sustainable growth. CTA is calling on federal provincial governments to provide known/trusted trucking companies greater access to foreign labour so newcomers to Canada can learn to become professional truck drivers from safe and labour-compliant fleets;
* The pandemic has brought to the surface a preexisting problem in trucking –
the growth of unscrupulous trucking fleets who use the underground economy, cheat on tax and labour rules and sidestep safety regulations to lower operating costs and attract drivers away from safe and compliant fleets. CTA is asking the government to broaden national enforcement against the practice – known as Driver Inc.
Governments and the supply chain must continue to work together to keep Canada moving.
Oregon Fine Rises For Trucks Failing To Use Tire Chains
The Oregon fine for trucks failing to use chains when required is rising this fall under a new Oregon law taking effect Sept. 25.
Prepare for slippery weather travel now! Oregon law requires all commercial vehicles to carry chains whenever road conditions might require their use during your trip and signs are posted.
The law also requires vehicles to chain up when signs tell you that conditions ahead require them.
Start carrying chains before the weather takes you by surprise. And before every trip, visit TripCheck.com for current road and weather conditions and more on Oregon chain requirements.
Cost of trucks without chains
The estimated cost of delays caused by trucks failing to follow Oregon chain laws is over $8 million a year – to the motor carrier industry and other highway users. When a truck loses traction, it can not only delay its delivery but also delay everyone else on the road behind a stuck truck.
Keeping Oregon moving is so important to motor carriers and all Oregonians that the 2021 Oregon Legislature raised the fine for trucks failing to use chains to $880. That law takes effect Sept. 25.
If a truck is involved in a crash where failure to use chains is a factor, there could be other costs for the motor carrier – not to mention other travelers.
Don’t be the driver stopping miles of traffic behind you! The time it takes to chain up will get you to your destination faster and reduce the chances of a costly delay.
OOIDA: Supply Chain Dysfunction Is Nothing New For Truckers
Washington DC… The Owner-Operator Independent Drivers Association issued the following response after the White House meeting on October 13th the Supply Chain Crisis:
Todd Spencer, president and CEO:
Truckers have been working tirelessly to keep the country safe and productive throughout the COVID-19 pandemic. They have already been operating around the clock, but are often restricted by factors beyond their control such as excessive detention time and the lack of readily-available, safe parking for their trucks. These problems must finally be addressed if the Administration hopes to implement any significant supply chain solutions. Most of what we are seeing is not a surprise to our members who have been plagued with dysfunction in the supply chain for decades and it’s not realistic to expect the supply chain will suddenly operate efficiently on a 24/7 schedule when drivers aren’t being fully paid for their time.
In recent months, global supply shortages have forced some truckers off the road. Drivers are experiencing the domino effects of supply and staffing shortages which are preventing them from complying with federal regulations. Examples include drug and alcohol testing delays and difficulties finding replacement electronic logging devices, DEF filters, and CPAP machines. We
encourage the U.S. Department of Transportation and other agencies to begin making some emergency allowances to keep safe, qualified drivers in business.
But let’s be clear, the current supply chain crisis is not due to a shortage of truck drivers! Because the real bottlenecks in the supply chain occur at pickup and delivery points, adding more trucks and drivers will simply makes the lines longer, NOT faster. Every region of our country and segment of our economy relies upon long-haul truck drivers and it’s time that both the government and the trucking industry begin treating them as essential workers. We support the Administration’s efforts to improve the quality of trucking jobs, but this must start with valuing and compensating all of a driver’s time.
The Owner-Operator Independent Drivers Association is the largest national trade association representing the interests of small-business trucking professionals and professional truck drivers. The Association currently has more than 150,000 members nationwide. OOIDA was established in 1973 and is headquartered in the greater Kansas City, Mo. area.
OOIDA Sends Letter To The U.S. Department of Commerce
The Honorable Gina Raimondo
Secretary
U.S. Department of Commerce
1401 Constitution Ave NW
Washington, DC 20230
Dear Secretary Raimondo:
The Owner-Operator Independent Drivers Association (OOIDA) is the largest trade association representing the views of small-business truckers and professional truck drivers. OOIDA has over 150,000 members located in all fifty states that collectively own and operate more than 240,000 individual heavy-duty trucks. OOIDA’s mission is to promote and protect the interests of its members on any issues that might impact their economic well-being, working conditions, and the safe operation of commercial motor vehicles (CMVs) on our nation’s highways.
The International Trade Administration’s Advisory Committee on Supply Chain Competitiveness recently recommended that the Department of Commerce “take a leadership role to coordinate federal agencies to immediately address the driver shortage that threatens the effectiveness of the nation’s critical supply chains.” As the largest trade association representing small-business truckers and professional truck drivers, our members reject the notion of a mythical driver shortage, especially claims of one at an “all-time high.”
In reality, evidence from the federal government and industry analysis show that driver turnover is the problem. For one, the Federal Motor Carrier Safety Administration (FMCSA) estimates that over 400,000 new commercial driver’s licenses are issued every year.1 On top of that, the U.S. Department of Labor did not find indications of a driver shortage when examining the issue in 2019. Instead, they identified the high turnover experienced by large carriers as one reason for the perception of a shortage.2 Reporting from representatives of the nation’s largest truck fleets routinely report annual turnover rates above 90%.3 Clearly, there is no shortage of drivers entering the industry.
1 FMCSA, Regulatory Evaluation of Minimum Training Requirements for Entry-Level Commercial Motor Vehicle Operators Final Rule, Federal Motor Carrier Safety Administration (Nov 2016), pg. 39
2 Stephen V. Burks and Kristen Monaco, "Is the U.S. labor market for truck drivers broken?," Monthly Labor Review, U.S. Bureau of Labor Statistics, March 2019, https://doi.org/10.21916/mlr.2019.5.
3 https://www.trucking.org/news-insights/turnover-remained-unchanged-large-truckload-fleets-fourth-quarter
For decades, our country’s largest motor carriers and the trade associations that represent them have perpetuated the myth of a driver shortage to promote policies that maintain the cheapest labor supply possible. We encourage the Department of Commerce to follow the Department of Transportation’s (DOT) lead and finally focus on improving driver retention to address supply chain disruption rather than expanding driver pools. Last month, DOT Secretary Buttigieg along with Department of Labor Secretary Walsh convened a roundtable with trucking industry representatives to discuss best practices about prioritizing retention and limiting turnover. They consistently heard from motor carriers, drivers, safety advocates, labor organizations, and academic researchers about making the profession a more rewarding, long-term career – there is no shortage of work that must be done in that regard.
A few areas that need urgent attention from federal regulators and lawmakers include increasing truck parking capacity, providing fair levels and methods of compensation, repealing the exemption that denies truckers guaranteed overtime pay, better driver training programs, and eliminating excessive detention time. For instance, a majority of OOIDA members who operate under the 60 hour/7-day rule and those who operate under the 70 hour/8-day rule spend between 11 and 20 hours each week waiting to load or unload their truck.4 Additionally, drivers are allocating more and more of their on-duty time searching for safe parking locations due to capacity shortfalls in every region of the country. Addressing these inefficiencies will repair supply chain vulnerabilities in a far more sustainable manner than simply allowing more drivers to enter the industry.
4 Owner-Operator Independent Drivers Association Foundation, 2018 Detention Time Survey (Jan 2019).
Since the roundtable, DOT leadership and industry stakeholders have continued their discussions about retention. FMCSA’s Motor Carrier Safety Advisory Committee (MCSAC) is working on formal recommendations related to the recruitment and retention of drivers. FMCSA’s newly created Driver Subcommittee will provide MCSAC with specific ideas. Unlike the International Trade Administration’s Advisory Committee on Supply Chain Competitiveness, the MCSAC Driver Subcommittee is comprised entirely of trucking industry representatives. We believe the Administration’s Supply Chain Disruptions Task Force should take this expertise into account when implementing any proposals that will impact the nation’s professional driver fleet.
OOIDA is eager to work with Executive Agencies on strategies that will help make trucking a more viable and rewarding career choice for Americans who are prepared to enter the driver workforce. The Department of Commerce along with the Administration’s Supply Chain Disruptions Task Force must prioritize resolving the underlying circumstances that have led to excessive churn. Otherwise, we anticipate turnover rates will remain precariously high or even increase no matter how many new drivers are eligible to enter the industry. We would welcome any opportunity to further discuss these issues with you and other Department of Commerce officials at your convenience.
Thank you,
Lewie Pugh
Executive Vice President
Owner-Operator Independent Drivers Association, Inc.
Wreaths Across America Proudly Announces Remember, Honor, Teach and Learn Award Winners
COLUMBIA FALLS, ME… The mission of Wreaths Across America (WAA) is Remember the fallen, Honor those that serve and their families, and Teach the next generation the value of freedom. Although most people will know the organization best as the folks who lay wreaths at Arlington Nation Cemetery on December 18th this year, The WAA mission is year-round and supported by the efforts of thousands of dedicated local volunteers throughout America.
Each year, WAA recognizes some truly outstanding individuals with our national Remember, Honor, Teach and Learn Awards. These award recipients are chosen from recommendations by our volunteer base and staff, culminating in an extensive review process by the WAA Executive Leadership Team. Other awards include the Jim Prout Spirit of Giving Award which is chosen by the WAA Logistics Team based on recommendations from wreath truck drivers, volunteers and staff and the Founders Award which is an honor bestowed by the Worcester family and our Founder, Morrill Worcester for appreciation of outstanding contributions in the effort to honor our nations veterans.
On July 24th at the WAA museum and headquarters in Maine, WAA proudly announce this year’s Remember, Honor, Teach and Learn Award winners.
And the winners are:
Remember Award: Given to an individual or group who REMEMBERS the fallen and their sacrifice in a way that goes above and beyond. This year’s recipient is Fran Haasch Law Group based in Florida.
The Fran Haasch Law Group has long been a supporter of efforts to raise funds and awareness for WAA’s mission in Florida. “Whether it is donating funds to sponsor wreaths to ensure as many veterans are remembered as possible each December, or her time, Fran ‘gets it’,” said Randy Lewer, WAA Board Member and Volunteer Location Coordinator for Florida National Cemetery. “She, and her whole team, really understand why it is so important to remember our nation’s veterans and honor their service and sacrifice. She is a passionate supporter, dedicated leader in the community and someone I am honored to consider a friend.”
Teach Award: Given annually to an individual or group who has made a large contribution in TEACHING the next generation to Remember and Honor those who serve in our nation’s military. This year’s recipient is PenFed Credit Union based in Pennsylvania. Company CEO James Schenck proudly accepted the award.
"PenFed is honored to receive this award on behalf of our more than 3,000 financial professionals and 2.3 million members,” said James Schenck, president/CEO of PenFed Credit Union and CEO of PenFed Foundation. “We are passionate about ensuring the men and women who defended our nation's freedoms are honored and remembered. For the past two years, we’ve participated in the wreaths escort and have been moved by the words of veterans, supporters and participants who shared what Wreaths Across America means to them. It’s an honor to continue teaching the next generation by telling the stories of our nation’s heroes and their families.”
Learn Award: Given semi-annually to a young individual who has learned, and understands, the Wreaths Across America mission and incorporates it into their young life. This year’s recipient is 18 year old Brady Kirk of Maine.
“The Learn Award is something we developed back in 2015 as a way to express the importance of not only teaching as part of the mission, but for youth to LEARN what it means to serve and sacrifice for this country and then use that knowledge in their own young lives,” said Wayne Hanson, Chairman of the Board, Wreaths Across America. “It has been our honor and privilege to watch Brady literally grow up in front of us over the last decade, and knowing he has taken what he’s learned and has chosen to serve his community makes me and the entire WAA family very proud.”
Jim Prout Spirit of Giving Award: Named in memory of James Prout, owner of Blue Bird Ranch Trucking of Jonesboro, Maine. Prout was the first person to volunteer to haul wreaths to Arlington when the program was in its infancy. The Award is given annually to a deserving professional truck driver or carrier that has supported charitable causes in a way that will positively affect generations to come. This year’s recipient is Bennett Transportation headquartered in Georgia. Lee Gentry accepted the award on behalf of the organization.
“Wreaths Across America holds a special place in the hearts of the truck drivers, agents and employees of the Bennett Family of Companies,” said Lee Gentry. Many of our team have served our country, have family members currently serving, or have known someone who paid the ultimate sacrifice for our freedom. As part of our commitment to Patriotism, we have embraced the cause of Wreaths Across America - and of the National Cemetery that is closest to our company, Andersonville National Cemetery. It is our great honor to be a part of the Wreaths Across America family, to continue to Remember, Honor and Teach those around us about the brave men and women who we recognize during the holidays and at events like this throughout the year. On behalf of the entire team, we are humbled and grateful for this special honor.”
Upcoming Award Announcements:
Honor Award: Given annually to an individual or group who HONORS those who serve and their families in a way that supports the Wreaths Across America mission. This year’s recipient to be presented by Karen and Morrill in September at a Medal of Honor Society event being held in Boston.
Founders Award: Chosen by Wreaths Across America Founder Morrill Worcester, this award is presented to an individual or group who exemplifies the mission to Remember, Honor, and Teach, and shows active support of our nation’s military and veterans. This year’s recipient will be announced at a special event planned for Friday, Dec. 17, at event in Washington D.C the night before Wreaths Across America Day.
Help support the wonderful efforts of these amazing people by sponsoring a veteran’s wreath anytime for $15 at www.wreathacrossamerica.org. Each sponsorship goes toward a live, balsam wreath that will be placed on the headstone of an American hero as we endeavor to honor all veterans laid to rest at noon on Saturday, December 18, 2021, as part of National Wreaths across America Day.
TMC/FleetNet America Find Decrease in Frequency of Unscheduled Roadside Events
Cleveland, OH… American Trucking Associations’ Technology & Maintenance Council said the council’s second quarter 2021 TMC/FleetNet America Vertical Benchmarking Program found an industrywide decrease in the frequency of unscheduled roadside maintenance.
“We continue to be pleased to offer TMC fleet members this information on the frequency of unscheduled roadside breakdowns by VMRS system. The ongoing series demonstrates that fleets can improve their breakdown performance if they follow the lead of best-in-class fleets in each of the vocational segments tracked,” said TMC Executive Director Robert Braswell.
The TMC/FleetNetAmerica survey found that during the first quarter of 2021, fleets averaged 31,638 miles of operation between unscheduled road repairs – up 7.2% from 29,506 in the first quarter of 2021.
Truckload carriers averaged 23,769 miles between breakdowns, an 8.8% increase in miles from the previous quarter. The time between breakdowns for LTL carriers increased to 46,186 miles in the second quarter from 44,380 in the first quarter of 2021. The tank sector saw a slight improvement, running 18,241 miles in the second quarter, up from 17,420 in the previous quarter.
“The data tells us that if, for example, the truckload carriers running the average miles between breakdowns could reach best-in-class performance, they would increase their miles between breakdowns by 64%,” said Emily Hurst, manager of data and analytics at FleetNet America, “and that would result in overall lower costs.”
The data indicates that the maintenance practices of the best-in-class fleets in each vertical resulted in lower costs for those fleets. For example, the leading fleet in the tank vertical operated more than twice as many miles between roadside breakdowns than the average for the tank vertical.
Understanding the frequency of roadside failures, and how a fleet’s experience compares to similar operations, can help maintenance leaders identify opportunities to improve their operations and reduce their maintenance expense.
The TMC/FleetNet Vertical Benchmarking Program is a benefit for TMC fleet members. In addition to the executive summary, which is available to TMC members, fleets that participate by sharing their data are provided an analytic tool that allows them to drill into their data, comparing it to the industry average.
Interested parties may also purchase copies of the report from TMC. Visit ATA Business Solutions for more information.
The program is a strategic collaboration between TMC/ATA and FleetNet America and is open to TMC fleet executive level members and FleetNet customers. The analytics provided via the program will be cumulative and non-fleet specific. For information about the TMC/FleetNet Vertical Benchmarking Program, visit https://benchmarkit.fleetnetamerica.com.
Ribbon-Cutting Ceremony for American Trucking and Industry Leader Hall of Fame Opens with First Inductees Announced during the American Truck Historical Society’s 50th Anniversary Celebration
KANSAS CITY, MO… – Four big names in the trucking industry will be inducted into the American Trucking and Industry Leader Hall of Fame (ATIL HoF) on Friday, October 15, 2021.
* Clessie Lyle Cummins, founder of the Cummins Engine Co.,
* Jack and Gus Mack, founders of Mack Trucks, Inc.,
* Owner-Operator Independent Drivers Association, and
* Dave Nemo, trucking icon.
A ribbon-cutting ceremony officially announcing the opening of the ATIL Hall of Fame by the Greater Kansas City Chamber of Commerce is on Friday, October 15, 2021.The inaugural ATIL Hall of Fame Induction Ceremony will be held in conjunction with the American Truck Historical Society’s 50th Anniversary celebration at the ATHS home office in Kansas City. Local and state dignitaries, along with trucking industry leaders, are invited.
The ATIL HoF is housed within the American Truck Historical Society (ATHS) in Kansas City, Missouri — the crossroads of America. “This is a wonderful opportunity for visitors to learn both about the history and pioneers of this great industry through both ATHS and the ATIL Hall of Fame, says Tom Mullen, ATIL HoF Chair.
On Saturday, October 16, ATHS celebrates its 50th Anniversary with an Open House, inviting its members to visit the Zoe James Memorial Library, the Visitor’s Center, and the newly developed American Trucking Industry and Leader Hall of Fame.
American Truck Historical Society milestones
March 1971: ATHS was founded in Dearborn Heights, Michigan, relocated to Birmingham, Alabama in 1977, and in 2001, moved to Kansas City, Missouri, where it is today.
October 1972: ATHS is recognized as the authorized organization to collect/preserve trucking history. Today the ATHS houses the Zoe James Memorial Library, which hosts a collection of more than 100,000 digitized and original photographs, 35,000 pieces of sales literature, and 45,000 books and periodicals.
October 1980: The first Wheels of Time magazine is published.
1972: First annual convention.
1980: First historic truck show. The shows have grown from 23 trucks in 1980 to over 1,000 trucks today! The ATHS National Convention & Truck Show now rotates between four U.S. locations.
May 2021: To honor the trucking industry and the companies and professionals who have gone above and beyond, ATHS developed the American Trucking and Industry Leader Hall of Fame (ATIL HoF). The trucking industry is crucial to the U.S. and its economic success.
October 15, 2021: A ribbon-cutting ceremony announcing the official opening of the ATIL HoF. The first ATIL HoF induction ceremony welcomes four icons.
“No transport industry Hall of Fame could exist without paying homage to these elite inductees. The impact they have on the industry is ongoing and everlasting. The American Trucking and Industry Leader Hall of Fame honors the pioneers of the trucking industry, whether they are drivers, company owners, or innovators to the industry,” said Mullen.
ATHS recognizes its 50th Anniversary Celebration sponsors: Hagerty Insurance, Vander Haag’s Inc., Bridgestone, Inland Truck Parts & Service, Sercombe Trucking Co., and Big Rig Upholstery. For details about the celebration, visit the ATHS website at ATHS.org/50thAnniversary.
The American Trucking and Industry Leader Hall of Fame (ATIL HoF) was formed in May 2021 to showcase corporate and association award programs, along with individual trucking industry leaders. By bringing the best of the best awards programs to one location—transport industry workers, their families and those who have a passion for trucks, its people, and the industry, are able to experience first-hand the history of and pride for the trucking industry as a whole. ATIL HoF is housed within the American Truck Historical Society’s in Kansas City, Missouri. For more information visit ATILHallofFame.org
The American Truck Historical Society (ATHS) was formed to preserve the history of trucks, the trucking industry, and its pioneers. ATHS is international in scope, with almost 20,000 members and 100 chapters spanning 23 countries and all 50 United States. ATHS has almost 100 chapters. The Zoe James Memorial Library hosts a collection of over 100,000, digitized and original photographs; 35,000 specimens of sales literature, more than 45,000 books and periodicals, along with an extensive collection of scale model trucks. The ATHS home office is located in Kansas City, Mo., U.S.A. More information about ATHS, including library hours of operation, can be found at ATHS.org
PA Turnpike Partners with Broadband Infrastructure Experts
HARRISBURG, PA… The Pennsylvania Turnpike Commission (PTC) is installing a large-scale fiber optic broadband network in the eastern part of its system to enhance its communications capacity. This network will increase bandwidth and boost connectivity between the agency’s administrative buildings and support automated tolling capabilities and other advanced telecommunications applications for improved customer safety and mobility. The 220-mile fiber optic network will extend broadband to underserved areas and generate non-toll revenue through a unique partnership with the private sector.
“This unique partnership will produce a fiber-optic infrastructure that will become an essential element for roadway monitoring and surveillance, allowing us to enhance safety and improve incident response on our system as well as set a foundation for rural broadband,” said PTC CEO Mark Compton. “It’s an important component of the PA Turnpike’s continuing efforts to move our intelligent transportation systems forward and to prepare for connected and automated vehicles to benefit not only customers and employees, but also emergency responders and neighbors.”
PTC has teamed with commercialization partners to generate revenue by leasing excess fiber-optic infrastructure to outside organizations, such as cellular network providers or other groups seeking high-speed broadband – proving that such network infrastructure can deliver parallel benefits that reduce the impacts of initial infrastructure investments. Cities and governing agencies are increasingly seeking creative, dual-purpose projects to answer the challenges posed by capital costs.
Construction began this spring along the eastern part of the Turnpike mainline from Harrisburg East Interchange to the New Jersey state line and on the entire Northeastern Extension (I-476). Completion of this section is estimated to occur during 2022. The western section is slated to be completed in 2026.
In 2020, PTC awarded Plenary Broadband Infrastructure (PBI) a long-term contract for the Fiber Infrastructure Operations, Maintenance and Commercialization Services project to operate and maintain the network and extend broadband capacity along 220 miles of the Pennsylvania Turnpike. The 25-year contract includes operations and maintenance services, as well as commercialization services for a fiber-optic broadband network. The PBI team includes: Tilson, and its asset owning affiliate, Tilson Infrastructure, a national network development and information infrastructure services firm, as the operations and maintenance contractor; and Plenary Americas as an equity investor, lead developer and financial arranger.
PBI and Tilson Infrastructure will commercialize dark fiber — infrastructure that is not yet “lit” or put into use — along the route and develop network infrastructure that will provide increased connectivity for the region. The network will enable customers including large enterprises, internet and telecom providers, cable multiple-system operators, municipalities, and educational institutions to expand their service areas and customer reach on direct, low latency routes across Pennsylvania.
“I’m excited to lead Tilson Infrastructure’s commercialization efforts as we team up with the Pennsylvania Turnpike to bring the benefits of broadband fiber — data speeds, highway safety, smart driving and internet accessibility — to travelers and unserved and underserved communities,” said Tilson Infrastructure’s Director of Fiber Business Development Ian Horowitz. “The new dark fiber provides carriers, hyperscalers, data centers, and internet service providers with the bandwidth needed to reach municipalities, universities, cell towers, poles, enterprise customers and others without the need to buy aging fiber or be faced with having the expense to build it themselves.”
“PBI is proud to partner with the Turnpike Commission to increase broadband capacity and accessibility through this innovative, long-term partnership,” said Plenary Americas Director of Project Delivery Ed Dice. “Our team is committed to providing reliable and highly responsive network services for the benefit of all Turnpike users and the broader, regional Pennsylvania market.”
Onboard Documentation and Supporting Documents
Motor carriers and drivers have specific requirements under the ELD regulations. Some of the most commonly cited violations pertain to the documents and materials drivers are required to have with them in the commercial motor vehicle (CMV), or that motor carriers must retain in their files, and provide to enforcement personnel upon request. Below are a few reminders to help motor carriers and drivers adhere to these requirements.
What ELD user documentation must be onboard a driver’s CMV?
A driver using an ELD must have an ELD information packet onboard the CMV containing the following items:
* A user’s manual for the driver describing how to operate the ELD;
* An instruction sheet describing the data transfer mechanisms supported by the ELD and step-by-step instructions to produce and transfer the driver’s hours-of-service records to an authorized safety official;
* An instruction sheet for the driver describing ELD malfunction reporting requirements and recordkeeping procedures during ELD malfunctions; and
* A supply of blank driver’s records of duty status (RODS) graph-grids sufficient to record the driver's duty status and other related information for a minimum of 8 days.
Can the ELD information packet be in electronic form?
Yes. The user’s manual, instruction sheet, malfunction instruction sheet, and supply of blank driver’s RODS graph grid can be in electronic form. A logging software app would meet the requirement for supply of blank RODS. This is in accordance with the FMCSA rule titled “Electronic Document and Signatures” published April 16, 2018 (83 FR 16210). See 49 CFR 390.32(b).
What are the supporting documents required in the normal course of business to verify a driver's records of duty status (RODS)?
They consist of five categories, described in 49 CFR 395.11(c):
* Bills of lading, itineraries, schedules, or equivalent documents that indicate the origin and destination of each trip;
* Dispatch records, trip records, or equivalent documents;
* Expense receipts related to any on-duty not-driving time;
* Electronic mobile communication records, reflecting communications transmitted through a fleet management system; and
* Payroll records, settlement sheets, or equivalent documents that indicate what and how a driver was paid.
Note: If a driver keeps paper RODS under 49 CFR 395.8(a)(1)(iii), the carrier must also retain toll receipts. For drivers using paper RODS, toll receipts do not count toward the eight-document cap.
What information should be in the supporting documents?
Supporting documents must contain the following elements:
* Driver name or carrier-assigned identification number, either on the document or on another document enabling the carrier to link the document to the driver. The vehicle unit number can also be used if it can be linked to the driver;
* Date;
* Location (including name of nearest city, town, or village); and
* Time.
How many supporting documents must be retained by motor carriers, and when must drivers submit them to the motor carrier?
Motor carriers must retain up to 8 supporting documents for every 24-hour period that a driver is on duty. Drivers must submit their RODS and supporting documents to the motor carrier no later than 13 days after receiving them.
If a motor carrier retains more than eight supporting documents, the motor carrier must maintain the first and last document generated during the regular course of business.
Are there specific categories of supporting documents that drivers can provide electronically?
Two categories—electronic mobile communications and payroll records—are not documents a driver would have to physically retain. They may be part of a larger record that the carrier retains electronically or physically at the dispatch location or principal place of business. In applying the eight-document limit, all information in an electronic mobile communication record will be counted as one document per duty day.
You can find this information, as well as questions and answers on many more topics in the ELD Frequently Asked Questions. Browse the topics or search for key terms.