Enerburn® & Diesel Fuel Additives For Preventive Maintenance
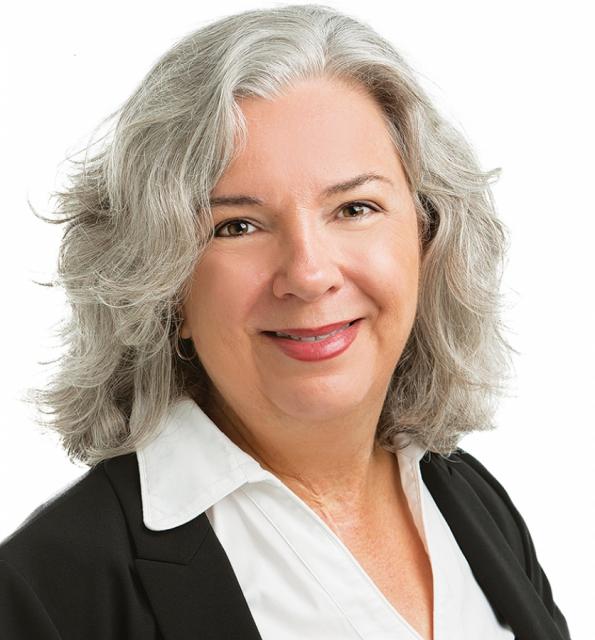
EnerBurn® is at the right place at the right time as a great fit in the vast array of readily available “after-market” fuel additives. It is growing increasingly common for diesel fleet managers, independent transport “owner operators” and diesel engine mechanics to turn to one or more fuel additive products as a preventive maintenance strategy. Business owners understand that savings on repairs and reducing downtime leads to sustainable profits. The judicious choice of fuel additives to prevent operational losses makes good business sense. But where do you start?
The key is in understanding the differences among fuel additives and how different types of additive ingredients can be used to address different problems. Fortunately, good information can be found on the internet; so you don’t have to be a chemist or a fuel expert. I always advise truck and fleet owners to conduct their own due diligence. For instance, product claims on the label should be substantiated by independent third party test data. If “proof of performance” data is not posted on the company website then try contacting them directly for more information – they should be willing to share any test reports or certificates that supports additive product claims. The vast majority of fuel additive products come from two sources, either manufacturers who either sell directly to businesses and/or consumers or 2nd-tier companies who buy from fuel additive manufacturers and distribute as their own brand under a private label. Regardless of the source fuel additive vendors are generally not required by law to prove the product claims so the expression “buyer beware” definitely applies.
In any case it is useful to arm yourself with knowledge of some fuel additive basics. I limit this to discussion of the three types of fuel additives that are generally recommended to keep diesel engines in good working order, call it engine preventive maintenance “best practices”. In my opinion these are: 1) combustion improvers and/or fuel combustion catalysts, 2) fuel lubricants, and 3) fuel stabilizers. These three types of fuel additive ingredients make up a “common-sense” foundation of preventive maintenance for any diesel engine. The goal being to help extend the life of engine components and reduce downtime. These three additive types should be used more or less continuously – that is, with every tank of fuel on each and every fill-up. This is distinct from those additive types that can help out on those occasions when the situation requires, for example the use of “anti-gel” and/or “anti-freeze” additives in extreme cold weather.
Fuel lubricant additives have become universally recommended by OEM’s since the introduction of ULSD (Ultra-Low Sulfur Diesel) in 2006; there are many different brands to choose from. Even though there is a fuel specification for lubricity that must be met by suppliers of no. 2-D & no. 1-D ULSD, this is not stringent enough to ensure the fuel has adequate lubricity for protecting diesel engines. This fuel lubricity specification is in accordance with D 975 and the specified maximum value is 520 microns. The standard test method for evaluating the lubricity of fuels is ASTM D 6079 in which a wear scar is produced on a metal sample by what is known as a High Frequency Rotating Rig (HFRR). A straightforward interpretation of the test is that the lower the number the smaller the wear scar and thus the better the lubricating property of the fuel. However, as stated in the ASTM literature, “it is not known that this test method will predict the performance of all additive/fuel combinations.” Nonetheless, a good strategy would be to select a fuel lubricant additive that has undergone testing of this type and produced results that were less than the minimum fuel specification of 520 microns by at least 10%-20%. The next step in the product evaluation would be to assess the cost per treated gallon of the additive as product pricing varies across brands. This is a simple preventive strategy that should help reduce friction and prevent wear and premature failure of fuel pump and fuel injectors.
OEM engine manufacturers have adopted high-pressure common rail fuel systems to more precisely control injector timing and create more uniform fuel injection profiles. At the same time fuel injector nozzle tips are machined with smaller holes that produce finer spray patterns. This is for the purpose of producing extremely fine fuel droplets (the technical term is “atomization”) that can better mix with air in the cylinder to maximize combustion efficiency. Under these conditions of high-localized temperatures and pressures (up to 30,000 psi) diesel fuel can react with itself to form gummy deposits that will clog the nozzles and disrupt the fuel spray pattern. This is also referred to as “coking” of the fuel and it can be worse for biodiesel blends that have inherently lower stability against oxidation. The formation of injector nozzle deposits, often referred to as Internal Injector Deposits (IID), can result in loss of engine power and higher diesel particulate emissions. Use of a fuel stabilizer additive will help prevent fuel injector nozzle fouling. Not only will a good fuel stabilizer additive prevent formation of IID it also will prevent stored fuel from degrading under most conditions.
If injector fouling is suspected then there are plenty of detergent-based “Fuel Injector Cleaner” type additives available. Periodic use of a good fuel injector cleaning product might also be a good preventive maintenance practice in addition to routine use of a fuel additive that has a fuel stabilizer will help prevent new deposits from forming.
The use of a good fuel borne catalyst (FBC) additive for diesel applications represents the 3rd plank in an engine owner’s “platform of preventive maintenance”. The diesel fuel treatment product EnerBurn® has a proprietary formula that includes both the FBC and fuel stabilizer additives. EnerBurn® has been proven to increase the burn rate of diesel thus directly improving the thermal efficiency of diesel engines by 5% – 12%. The benefit is substantially lowered soot levels and a correspondingly lower risk for maintenance issues caused by the accumulation of carbon deposits and soot. Tests performed by independent third parties both in the laboratory and field are conclusive in supporting the manufacturer’s claim of up to 70% reduced soot levels for in-service diesel engines. These results have been duplicated across various engine makes, models, and hours of service. Results can vary between 30% - 70% reduced particulate matter depending on conditions of engine load and rpm as can be expected. Summaries of some of these single engine tests are summarized on JKG Fuel Solutions website at http://betterdiesel.com/the-enerburn-experience/.
The direct benefits of improved fuel combustion that result from the consistent use of EnerBurn will more than pay for the added cost per treated gallon incurred. A big plus for owners of 2007 or newer diesel engines with DPF /DEF systems are extended intervals between active regenerations, fewer active regenerations and shorter active regeneration times.
When used according to instructions EnerBurn will substantially reduce the soot production on ALL diesel engines, both with and without DPF/DEF emissions control systems. Soot elimination is critical to extending the life of engine components (pistons, valves, rings, & cylinder). Eliminate soot from these moving parts and you have just eliminated the biggest contribution to engine wear caused by abrasion.
The FBC also lowers the burnout temperature of soot thus providing a cleaning and restoration effect for any in-service engine. This benefit for keeping “exhaust-side” components clean cannot be overstated. As any owner of a retrofitted DPF or 2007 or newer diesel engine can attest the EGR, EGR coolers, DPF, DOC, sensors, and turbo-chargers are all prone to fail pre-maturely due to excessive soot build-up. Regular use of EnerBurn is a proven strategy and saves thousands of dollars per vehicle per year for these expensive repairs.